A critical element of any efficient drainage system, gully gratings play a vital role in keeping our urban and rural landscapes free from excess surface water. Cast iron gully gratings, in particular, have long been valued for their durability and strength, effectively channeling water away from surfaces and into the underground drainage network. This comprehensive guide explores the world of cast iron gully gratings, conforming to BS EN standards, to help you understand their significance, types, and best practices for installation and maintenance.
Understanding Cast Iron Gully Gratings
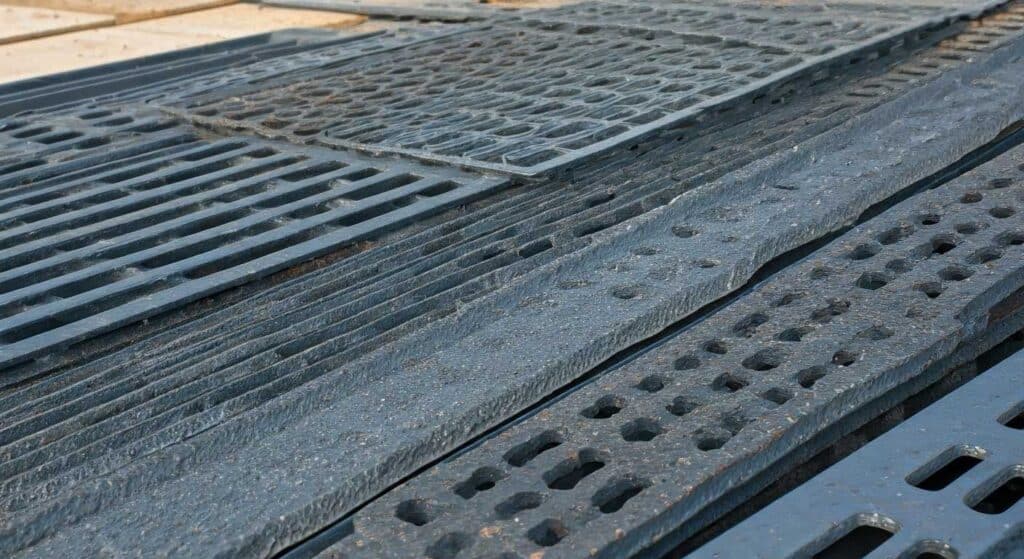
Cast iron gully gratings are robust components designed to withstand the test of time and heavy loads. They are manufactured using a process that involves pouring molten iron into molds, creating strong and durable gratings. The natural properties of cast iron, such as its high compressive strength and resistance to wear and tear, make these gratings ideal for demanding environments.
Beyond their strength, cast iron gully gratings are also known for their corrosion resistance. This inherent property ensures their longevity, even when constantly exposed to the elements and the corrosive nature of wastewater. The combination of strength, durability, and corrosion resistance makes cast iron a top choice for gully grating applications.
The Importance of Gully Gratings in Urban Infrastructure
Gully gratings form an integral part of urban infrastructure, efficiently managing surface water runoff and preventing potential hazards. Their primary function is to collect and direct rainwater and other surface water into the underground drainage system, ensuring the stability and longevity of roads, pavements, and other surfaces.
Particularly in areas with heavy rainfall or inadequate natural drainage, gully gratings are crucial in preventing flooding and waterlogging. Without these heavy-duty components, surface water could pool on roads and pavements, posing risks to pedestrians, cyclists, and vehicles.
Moreover, gully gratings help prevent debris, leaves, and other solid waste from entering and clogging the drainage system. This ensures a free flow of water and reduces the likelihood of blockages, which can lead to costly repairs and disruptions.
How Cast Iron Gully Gratings Work
Cast iron gully gratings are strategically positioned at low points along roads, driveways, and other paved areas. When rainwater or surface water flows across these surfaces, it is channeled towards the gully grating, often located along the kerbside. The grating’s design allows water to pass through its openings while preventing larger debris from entering the drainage system.
Beneath the grating lies the gully pot, a chamber that collects the water before it enters the underground drainage pipes. The gully pot traps sediment and debris, preventing it from flowing further into the drainage system and causing blockages. From the gully pot, the water flows through a network of underground drainage pipes, ultimately discharging into a watercourse, storm drain, or soakaway.
The perfectly crafted drainage system, of which cast iron gully gratings are a crucial part, ensures the efficient removal of surface water, safeguarding the integrity of urban infrastructure and preventing potential hazards associated with flooding and waterlogging.
Types of Cast Iron Gully Gratings Available
When it comes to cast iron gully gratings, there is no one-size-fits-all solution. Different applications require specific types of gratings based on load-bearing capacity, size requirements, and aesthetic preferences.
Two main categories of cast iron gully gratings are available: standard sizes and custom sizes. Each type caters to different project needs and ensures optimal performance in its intended environment.
Standard vs Custom Sizes
Standard size gully gratings are pre-manufactured with dimensions that cater to the most common requirements. These sizes are readily available from suppliers, offering a cost-effective and convenient solution for many projects. Standard sizes are suitable for applications where a perfect fit is not crucial, such as residential driveways, pavements, and car parks.
However, there are instances where a more bespoke approach is necessary. This is where custom size gully gratings come in. Manufactured to specific dimensions, custom sizes offer a precise fit for unique requirements, ensuring optimal performance and aesthetic integration. These are particularly useful for projects with unusual gully openings, heritage restorations, or specific design considerations.
Whether you choose standard or custom sizes, understanding your project requirements, such as the anticipated traffic load and the dimensions of the gully opening, is crucial in selecting the right type of cast iron gully grating for maximum storage duration and efficiency.
Load Classification and Its Relevance
Cast iron gully gratings are categorized into different load classifications, indicating their capacity to withstand varying levels of weight and pressure from pedestrian to vehicular traffic. The load classification system ensures that the chosen grating is suitable for its intended use, preventing potential damage or failure.
Each load class is denoted by a letter and a number, such as B125, C250, or D400. The letter represents the application area, with ‘B’ for pedestrian areas, ‘C’ for areas with occasional vehicular access like car parks, and ‘D’ for carriageways and hard shoulders. The number indicates the test load in kilonewtons (kN) that the grating can withstand. For example, a D400 grating is suitable for areas with heavy vehicular traffic, while a B125 grating is sufficient for pedestrian zones.
Selecting the appropriate load classification is critical for ensuring safety and preventing accidents. Using a grating with an inadequate load rating for a specific area can lead to structural failure, posing severe risks to vehicles and pedestrians. In high-stress environments such as airports and industrial sites, even higher load classifications, like F900, are utilized to withstand the immense weight of aircraft pavements and heavy machinery.
Installation and Maintenance Tips
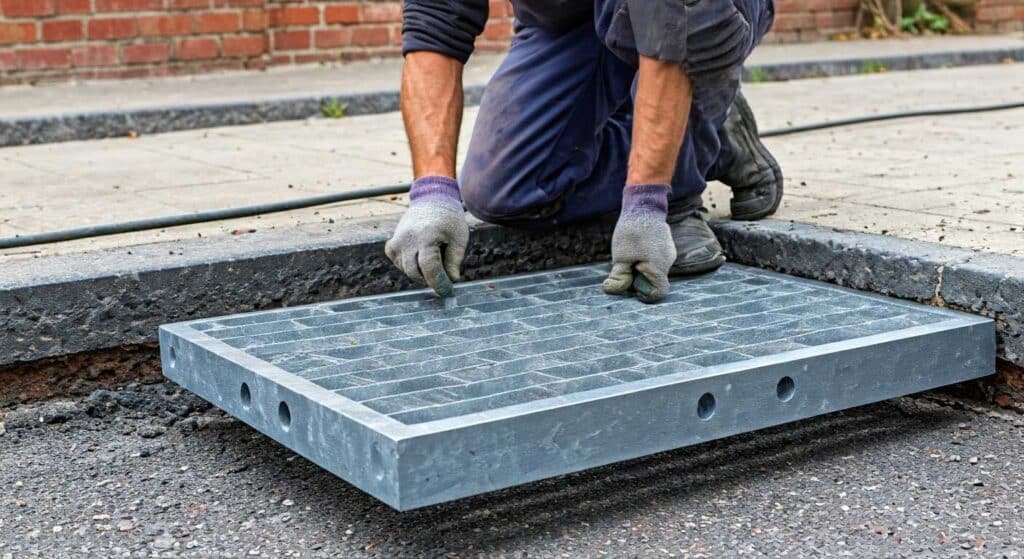
Proper installation and regular maintenance are crucial for ensuring the longevity, performance, and safety of your cast iron gully gratings. Incorrect installation can lead to various issues, including premature wear and tear, movement, and potential hazards for road users.
By following best practices and implementing a regular maintenance schedule, you can significantly extend the lifespan of your gully gratings, ensuring their optimal functionality for years to come. This proactive approach also minimizes the need for costly repairs or replacements down the line.
Best Practices for Installing Gully Gratings
Installing a gully grating correctly is vital for its stability and performance. It is crucial to ensure a level and secure fit within the gully opening, preventing any movement or rocking that can lead to damage or noise. This typically involves preparing a stable bedding material, such as concrete, around the base of the grating.
In addition to a secure fit, proper leveling is equally important. The grating should sit flush with the surrounding surface to prevent tripping hazards and ensure the smooth flow of water into the drainage system. This involves accurately measuring and adjusting the bedding material until the grating is level.
Furthermore, it is essential to consider the surrounding environment during installation. For instance, gully gratings in car parks should be installed to withstand vehicular traffic and potential impacts, while those in pedestrian areas might require anti-slip features for enhanced safety.
Maintenance Checklist to Prolong Lifespan
A simple yet effective maintenance regime is key to maximizing the lifespan and efficiency of your cast iron gully gratings. Regular inspections should be conducted to identify any signs of damage, wear, or blockage. This includes checking for cracks, chips, or missing sections in the grating itself, as well as clearing any debris that may be obstructing the water flow.
Debris removal is crucial to prevent blockages and ensure the grating’s maximum storage capacity. Leaves, litter, and sediment can accumulate over time, hindering the water flow and potentially leading to flooding or unpleasant odors. Regularly clearing the grating and the gully pot beneath it helps maintain optimal drainage and prevents costly issues down the line.
Furthermore, checking the condition of the surrounding bedding material is essential. Over time, the bedding material can deteriorate or shift, affecting the grating’s stability and level. Regularly inspecting and repairing the bedding ensures a secure and level fit, promoting longevity and preventing potential hazards.
Conclusion
Cast iron gully gratings play a critical role in urban infrastructure. Understanding their importance, types available, and installation tips is key to their longevity and effectiveness. Whether choosing standard or custom sizes, ensuring proper maintenance is vital. By following best practices and a maintenance checklist, you can prolong their lifespan. Consider the load classification and legal requirements for installations in the United States. For more insights on cast iron gully gratings and expert guidance on selecting the right option for your project, explore our Frequently Asked Questions section.
Frequently Asked Questions
What Are the Benefits of Using Cast Iron for Gully Gratings?
Cast iron’s durability makes it an excellent material for gully gratings, offering a greater lifespan than some alternatives. Their inherent weight deter theft, and their longevity requires less frequent replacement, saving on both costs and kerbside disruption.
How Do I Choose the Right Gully Grating for My Project?
Choosing the right gully grating hinges on its intended location. Motorways require high load classifications, while pedestrian areas can utilize lower ones. Matching the grating to the types of road and expected traffic ensures optimal performance.
Can Cast Iron Gully Gratings Be Recycled?
Absolutely! Both iron gully grates and ductile iron gully grates are recyclable. This minimizes their environmental impact and contributes to a sustainable approach to infrastructure development.
How Often Should Cast Iron Gully Gratings Be Replaced?
With proper maintenance, cast iron gully gratings can last several decades. Following a maintenance checklist and inspecting regularly help determine the lifespan and replacement needs, be it for a carriageway or footpaths.
Are There Any Legal Requirements for Installing Gully Gratings in the United States?
While the US doesn’t follow BS EN standards, local building codes and regulations will dictate kerbside drainage requirements. It’s crucial to consult these for proper installation procedures, similar to specifications for manhole covers.