Manhole covers are critical components of urban infrastructure, ensuring the protection of underground utilities while providing a safe surface for pedestrians and vehicles. Given their constant exposure to heavy traffic, extreme weather conditions, and external impacts, manhole covers must have high impact resistance to prevent breakage, deformation, or displacement.
To ensure their durability and safety, various impact resistance tests are conducted to evaluate how well manhole covers can withstand sudden or repeated forces. This article explores the different testing methods, factors affecting impact resistance, and the most suitable materials for high-performance manhole covers.
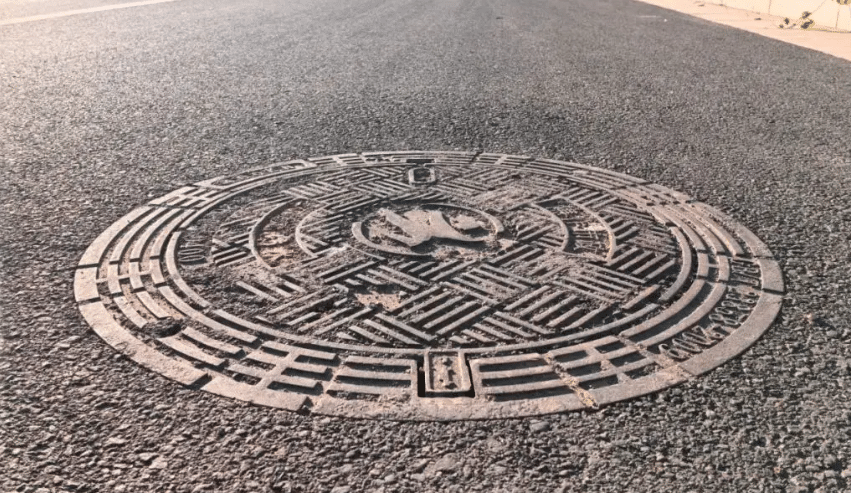
1. Importance of Impact Resistance in Manhole Covers
Manhole covers must endure repeated mechanical stress from vehicles, including trucks, buses, and other heavy loads. If the impact resistance is insufficient, the covers may:
- Crack or break, leading to dangerous open holes in roads.
- Shift or displace, increasing the risk of accidents.
- Wear out faster, resulting in higher maintenance and replacement costs.
For these reasons, manufacturers must rigorously test manhole covers to comply with international safety standards and ensure long-term performance.
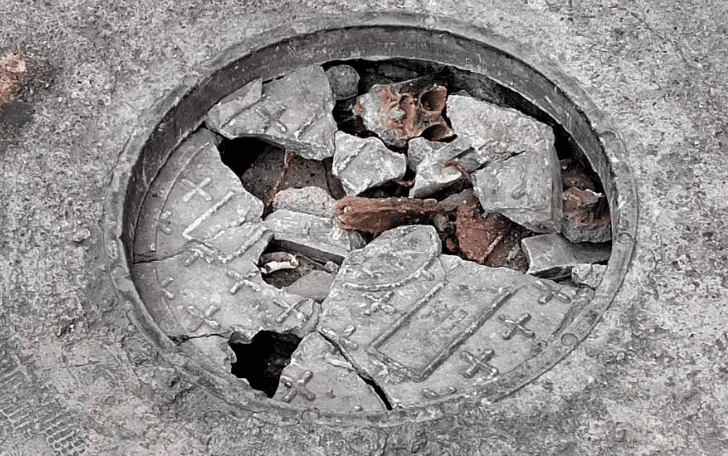
2. Testing Methods for Impact Resistance
2.1 Drop Weight Test
The drop weight test is one of the most common methods to evaluate the impact resistance of manhole covers. This test simulates a sudden, high-force impact, such as a heavy object falling on the cover or the impact of a vehicle tire at high speed.
Procedure:
- A heavy steel weight (typically between 5–10 kg) is dropped from a specific height onto the cover.
- The impact force is calculated based on the weight and height.
- The cover is then examined for cracks, deformation, or fractures.
Materials such as ductile iron and reinforced composite generally perform well in this test due to their ability to absorb energy without breaking.
2.2 Static and Dynamic Load Tests
In addition to impact resistance, load-bearing capacity is crucial for manhole covers. These tests ensure that the cover can handle both static and repeated dynamic forces.
- Static load test: A continuous force is applied to the cover to determine at what pressure it begins to deform or break.
- Dynamic load test: The cover is subjected to repeated forces to simulate real-world conditions such as vehicles driving over it thousands of times.
This test is particularly important for covers used in high-traffic roads and highways, where durability is essential.
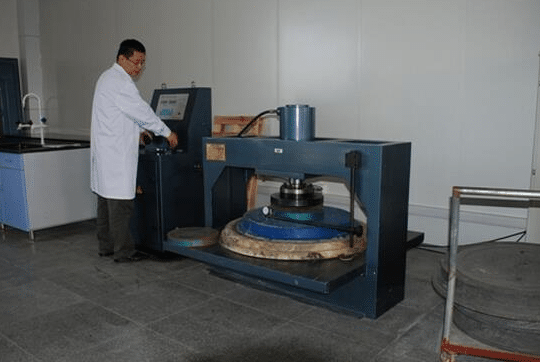
3. Factors Affecting Impact Resistance
3.1 Material Composition
Different materials offer varying levels of impact resistance. The most common materials used in manhole covers include:
Material | Impact Resistance | Weight | Durability | Cost |
---|---|---|---|---|
Ductile Iron | ⭐⭐⭐⭐⭐ | Heavy | High | Medium |
Composite Materials | ⭐⭐⭐⭐ | Light | High | Medium |
Reinforced Concrete | ⭐⭐⭐ | Very Heavy | Medium | Low |
- Ductile Iron: Excellent impact resistance, commonly used in high-traffic areas.
- Composite Covers: Lightweight and impact-resistant, often used in pedestrian areas.
- Reinforced Concrete: Good for low-traffic areas, but more susceptible to cracking under high impacts.
3.2 Thickness and Structural Design
The thicker the manhole cover, the better it can absorb impact energy. Many modern covers feature reinforced designs, including:
- Ribbed structures to improve load distribution.
- Double-layered composite materials for enhanced shock absorption.
- Anti-slip surfaces for improved safety.
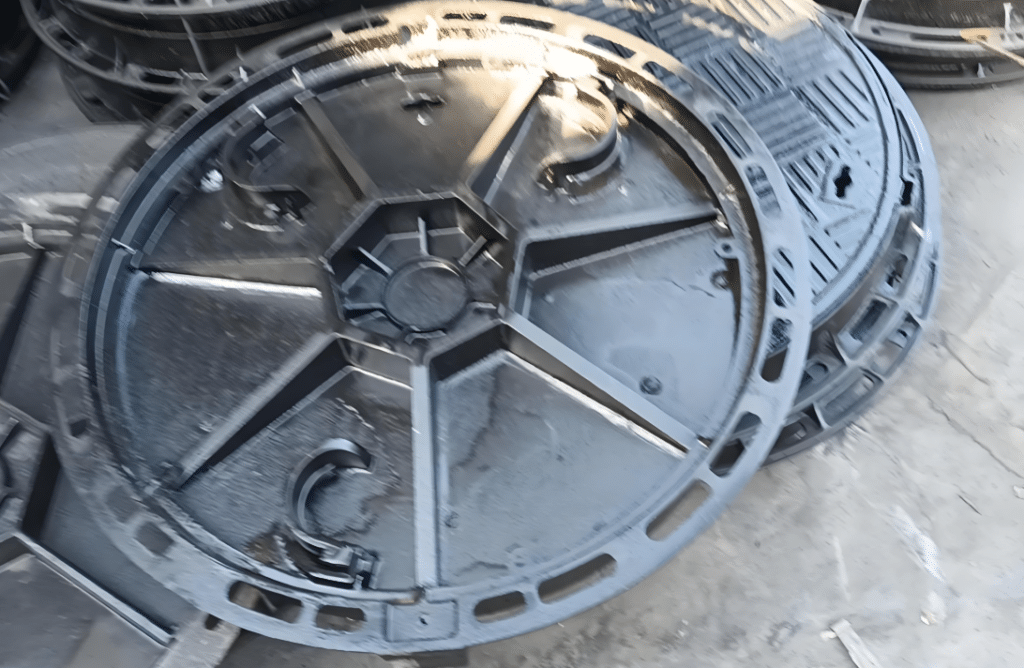
3.3 Environmental and Traffic Conditions
Manhole covers in different locations face varying levels of impact stress:
- Highways and industrial zones: Require maximum impact resistance due to heavy trucks and machinery.
- Urban streets and pedestrian areas: Need covers with moderate impact resistance and anti-slip surfaces.
- Extreme weather conditions: Rain, snow, and temperature changes can affect material strength over time.
To ensure durability, manufacturers often apply protective coatings such as asphalt layers or anti-corrosion treatments.
4. Compliance with International Standards
Impact resistance tests must comply with global safety and quality standards to ensure performance and durability. Key standards include:
- EN 124 (Europe): Classifies covers based on load-bearing capacity (A15 to F900).
- ASTM A48 (USA): Defines impact resistance for cast iron covers.
- ISO 1083: Sets standards for ductile iron materials used in manhole covers.
Manufacturers must meet these regulations to ensure safe and reliable performance in urban and industrial environments.
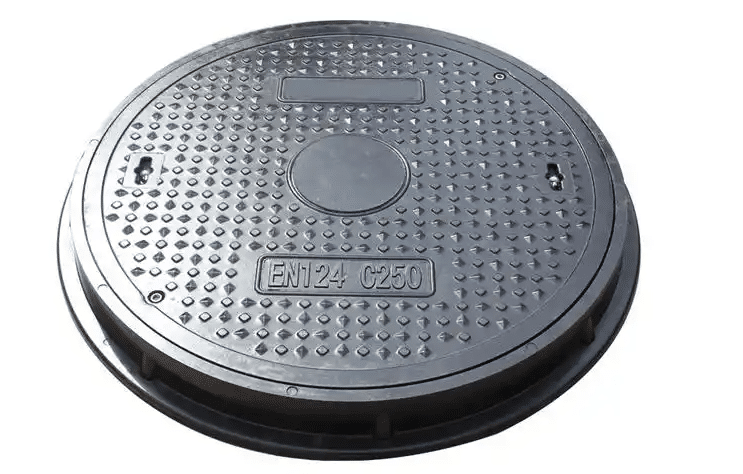
5. Conclusion
Impact resistance is a critical factor in ensuring the safety and longevity of manhole covers. Through rigorous drop weight tests, load-bearing assessments, and material innovations, modern manhole covers are designed to withstand high-impact forces without cracking or failing.
By selecting high-quality materials such as ductile iron or reinforced composites, and ensuring compliance with international safety standards, urban planners and engineers can guarantee the durability and reliability of manhole covers in any environment.
As technology advances, future innovations in lightweight, high-strength materials will further enhance the performance of manhole covers, reducing maintenance costs and improving urban safety.